Sustainability
Home / Sustainability
On the road to sustainability
For some years now, we have been on a path towards sustainability and waste reduction within the company.
We use resources wisely, reduce the amount of plastic in our packaging, pay more attention to the use of paper and make many other micro gestures every day in order to achieve a macro improvement.
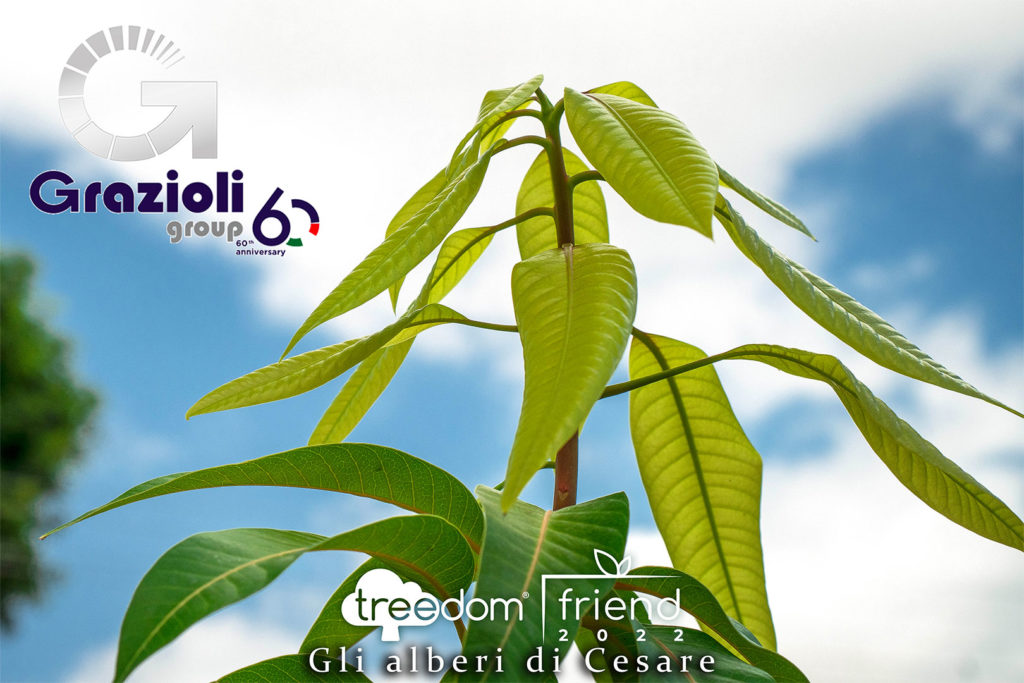
Treedom Project
Along the way, we decided to stop by our friends at Treedom, creating the “Gli alberi di Cesare” forest, to pay homage to the company’s founder Cesare Grazioli in the year of its 60th anniversary and add another eco-sustainable initiative to our journey.
From today, our customers will be able to plant trees in territories around the world with us, supporting local populations and offsetting CO2, in favor of a thoughtful and positive global growth.
If your business is an end in itself and harms someone in the world, where is the sense of growth?
The 4 R's of sustainability Grazioli Cesare
Sustainabilityis a term that today must be included in every aspect of the company, from waste management in administrative environments to the recovery of materials in production.
For this reason, over the years, Grazioli Cesare Srl has introduced changes and improvements in every area of the company, looking for waste and opportunities for reduction, reuse and recycling. The SDGs defined at global level are very ambitious goals and require a significant and constant evolutionary process over time. As they always say, ‘to get there, you have to start somewhere’. In line with this philosophy, at Grazioli we decided to take the first step by trying to adapt as much as possible to the 4 R’s of sustainability the industrial tube deformation machines we have been producing since 1962.
A process that has involved designers, technicians and operators in research and development at the highest levels, to maintain the quality guaranteed by the Grazioli brand and at the same time contribute to the battle to protect the planet. Today, after 3 years of research, we can say with pride and satisfaction that we have taken big steps in the right direction and, ahead of us, we have a very bright road that will lead us to the goal of full sustainability.
1. Reducing
When a company commits to to responsible and innovative choices that are efficient in terms of energy consumptionand theuse of materials and raw materials,it means that it is making an important effort to reduce its environmental impact by focusing on the use of environmentally friendly, clearly identifiable and easily recyclable materials, or on processes that reduce waste or energy consumption.
- Reducing electrical.
Green turn in the production of industrial tube deformation machines. The choice is to switch from a hydraulic power unit to an electric one, to cut energy consumption by 70% and eliminate the need for power unit lubrication. - Packaging.
We use recycled and recyclable wood packaging to transport and ship our finished machines. The plastic film that protects against the weather has also been reduced by 20% in the last 3 years. - Reducing waste.
Our production system allows the customer to use 95% of the bar material, thus limiting waste to a minimum.
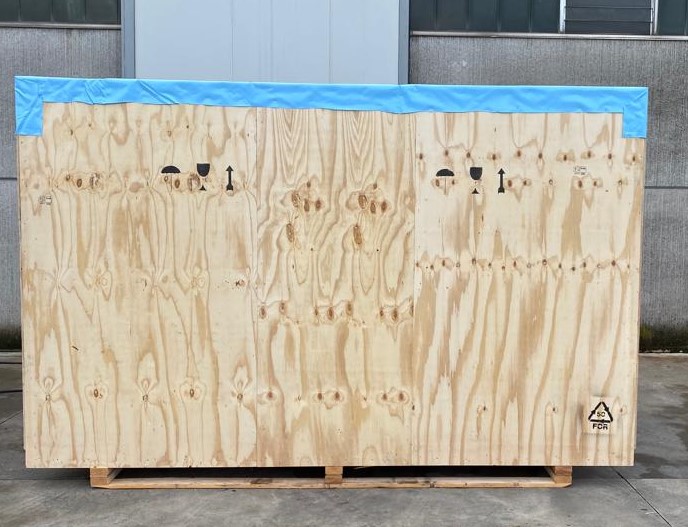
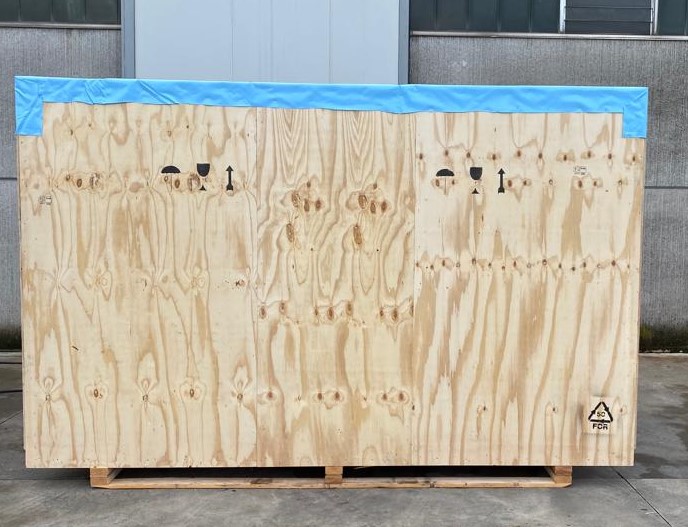
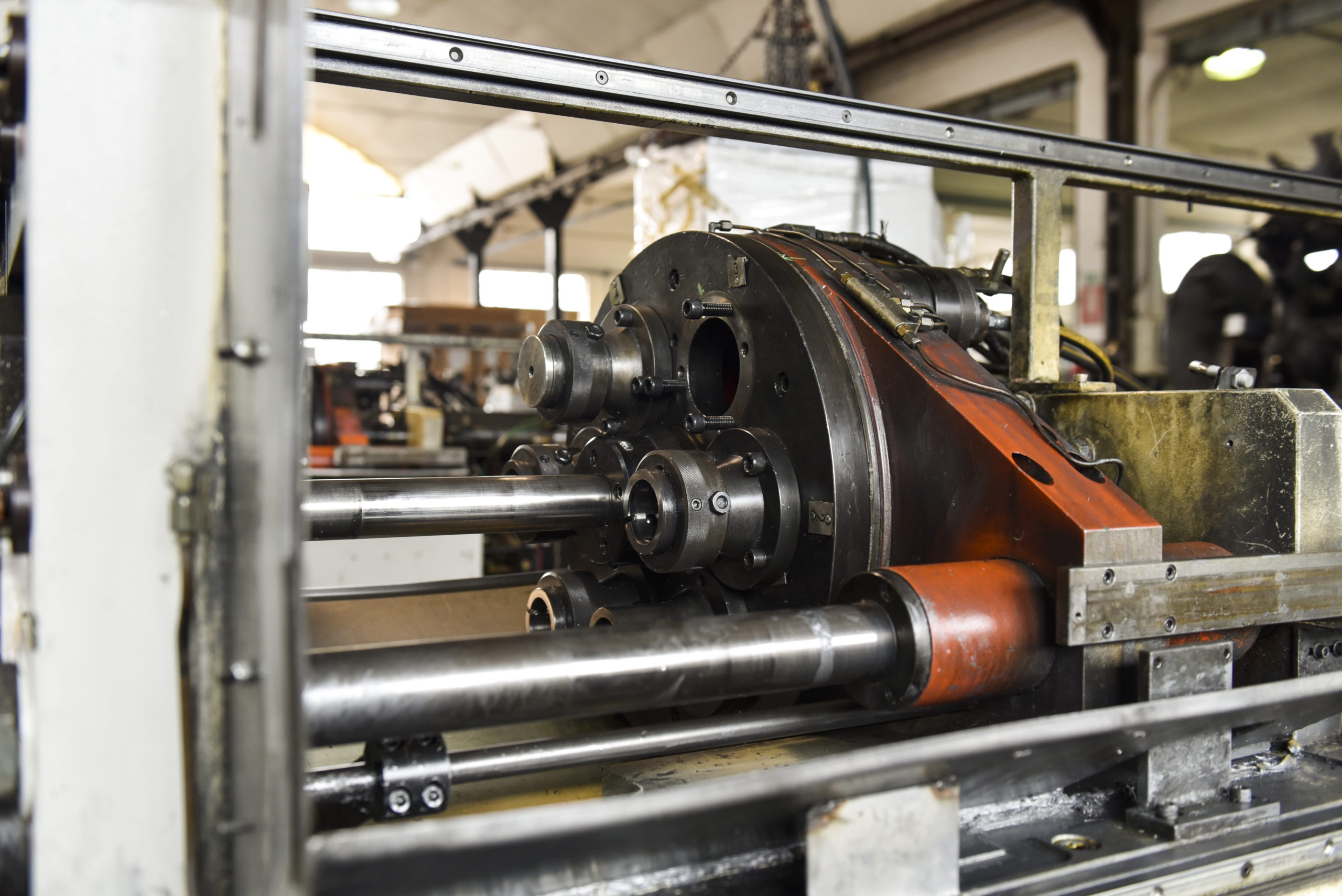
2. Reuse
In the course of our sustainability research and development, re-use has been the most difficult point to tackle. On the one hand, because our machines enter production processes that we cannot directly manage, and on the other hand, because giving a second life or using recycled materials inside the machines is a difficult task.
Despite these premises, we have found an effective way to respond to the R of reuse.
- Interchangeable tools
Through careful design of the machining tools, we have devised a universal coupling system that makes our tools interchangeable between one Grazioli machine and another.
Therefore, when a customer replaces a machine, they can reuse the tools they already have. - Revamping
Can a machine from 1998 be upgraded to meet the parameters of Industry 4.0? Our answer is YES!
Thanks to the revamping service we offer, we can update old machines, restoring their original production efficiency and adapting them to the parameters defined by current safety and digitalisation regulations.
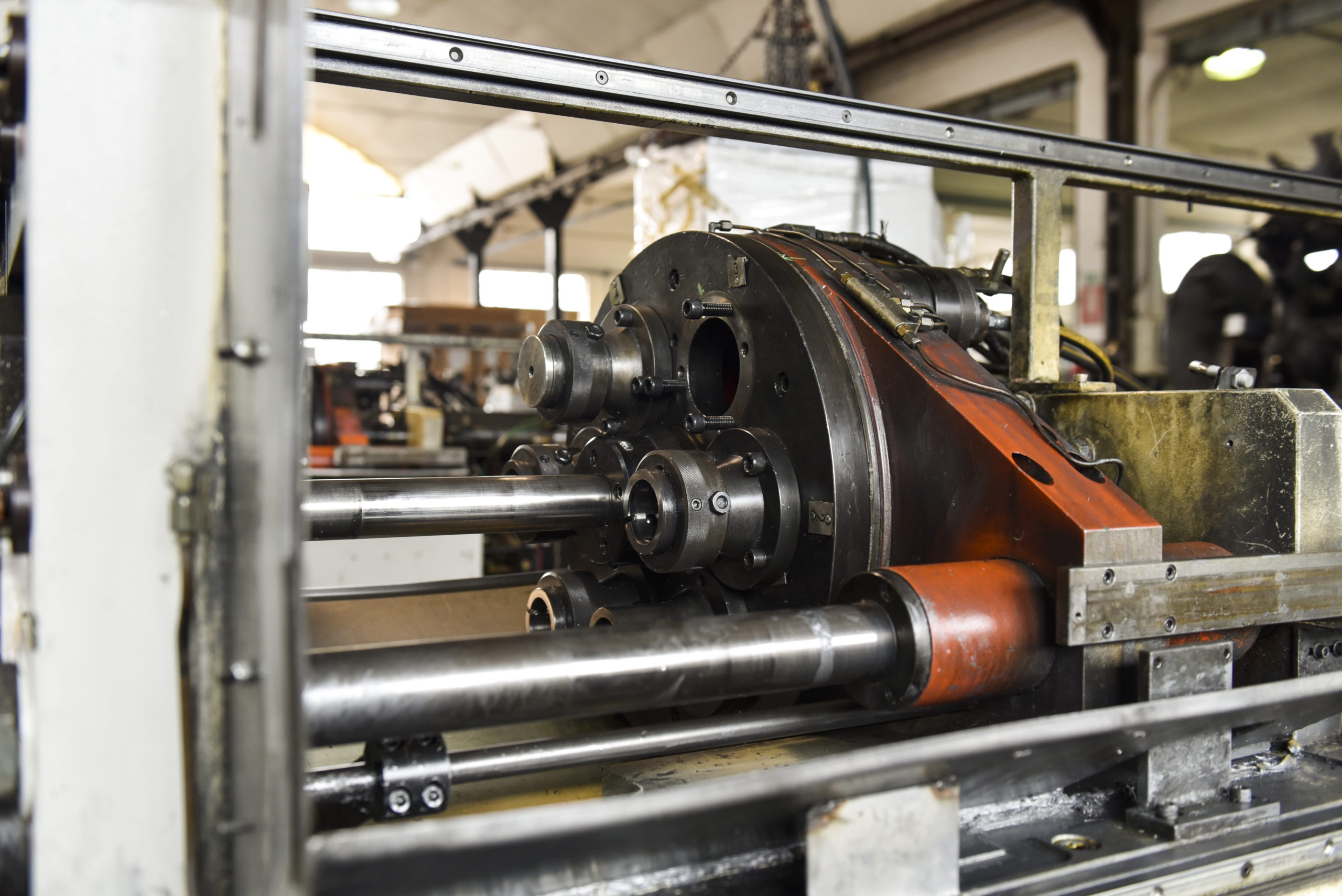
3. Recycling
The recycling system involves the entire production process and not just the final stage. In fact, a product must be designed with recycling in mind, using biodegradable materials. These facilitate natural disposal when the product becomes waste, avoiding materials that are more difficult or impossible to recycle.
Separate waste collection is a key step in the process.
It reduces the costs of treatment processes, especially for the environment.
- Lubrication oil
The lubrication oil used in our machines can be disposed of as waste oil without the need for purification processes to remove slag or foreign bodies.
Thanks to an internal decanting chamber filtering procedure, the oil – which works in a closed circuit – is always clean and free of slag. - Electrical material
All electrical material included in Grazioli tube forming machines can be disposed of according to the WEEE disposal procedure.
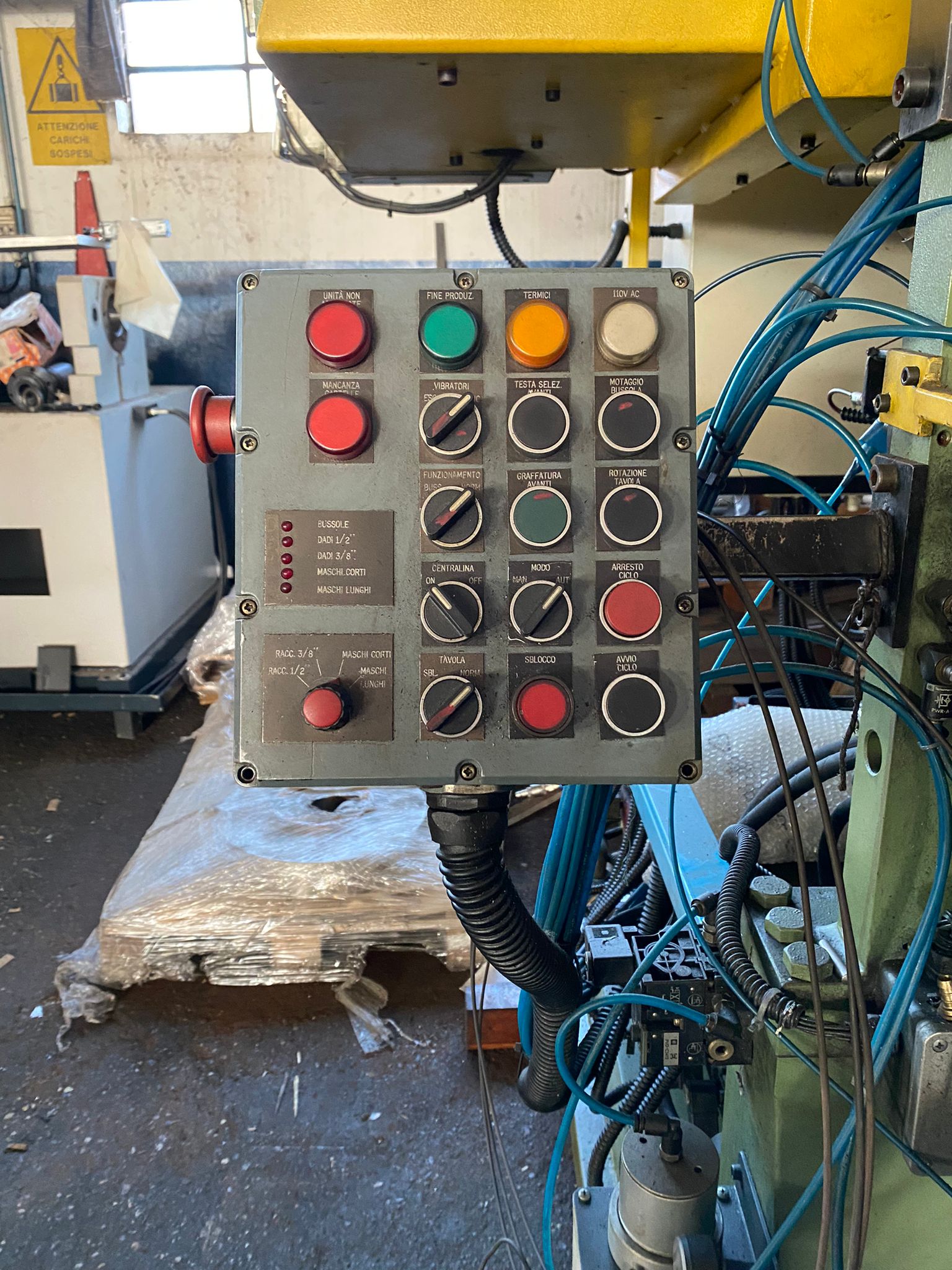
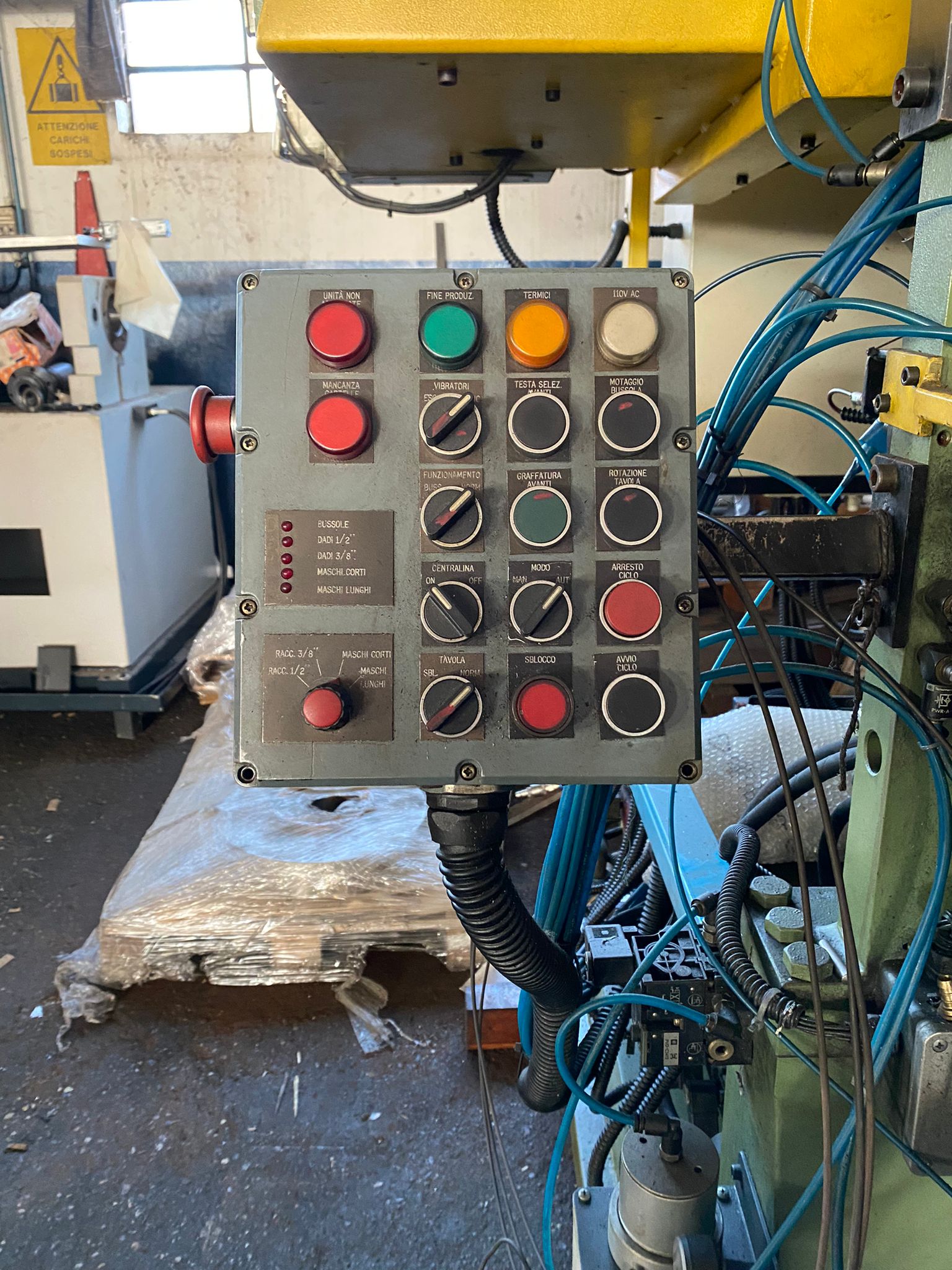
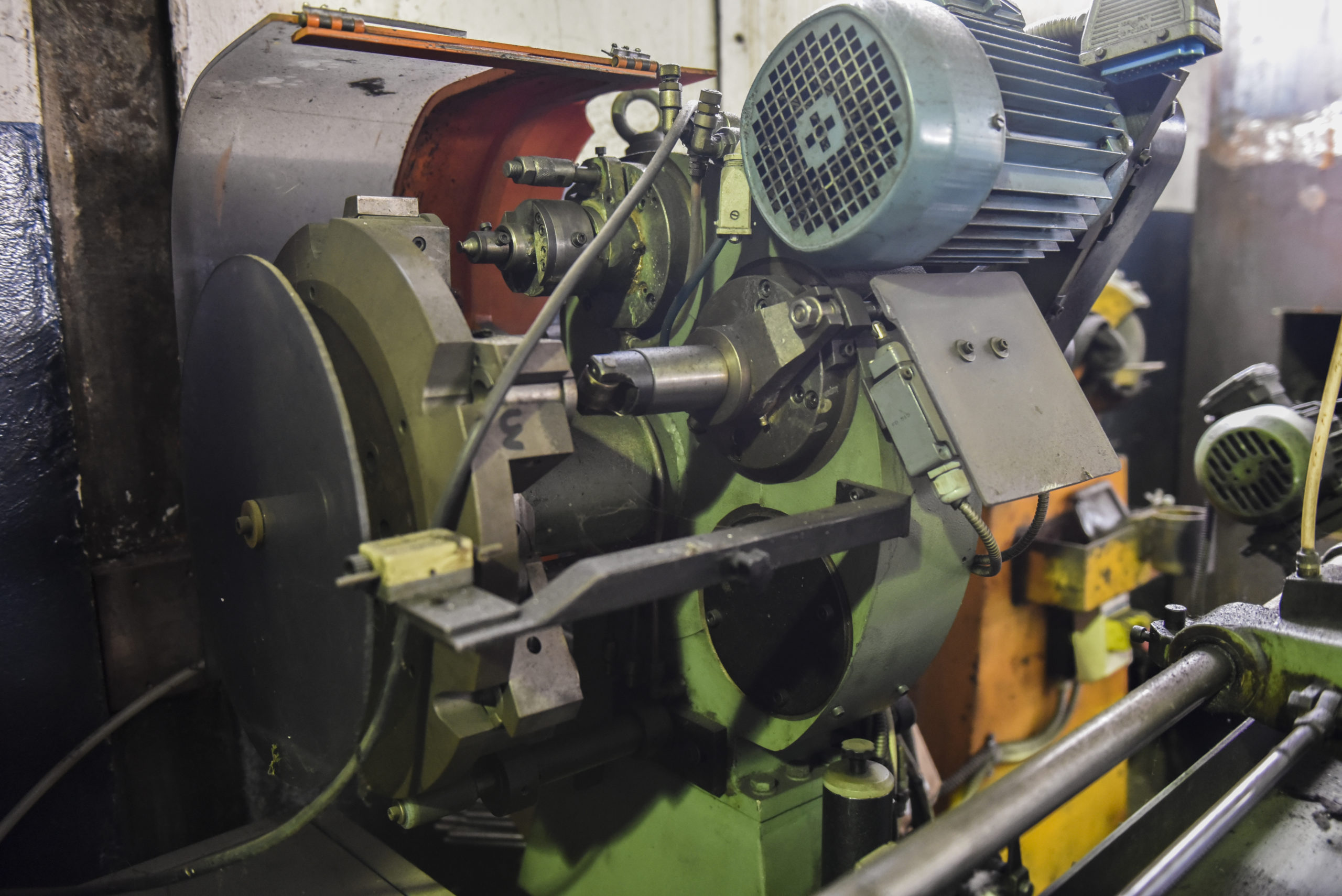
4. Recovery
At the end of the cycle of use and reuse of the product, when it is no longer usable as such, we cannot always obtain from it other materials to be used again. Therefore, we have focused on using the waste as fuel in waste-to-energy plants: burning it will reduce its bulk and produce energy.
- Clean energy
Following the separate disposal of the materials used, what remains of our machinery is inert waste that can be burnt in waste-to-energy plants. - Machinery buy-back
For a number of years now, we have been buying back machinery manufactured over 30 years ago from our customers. The aim is to create little glimpses within the company of our 60-year history.
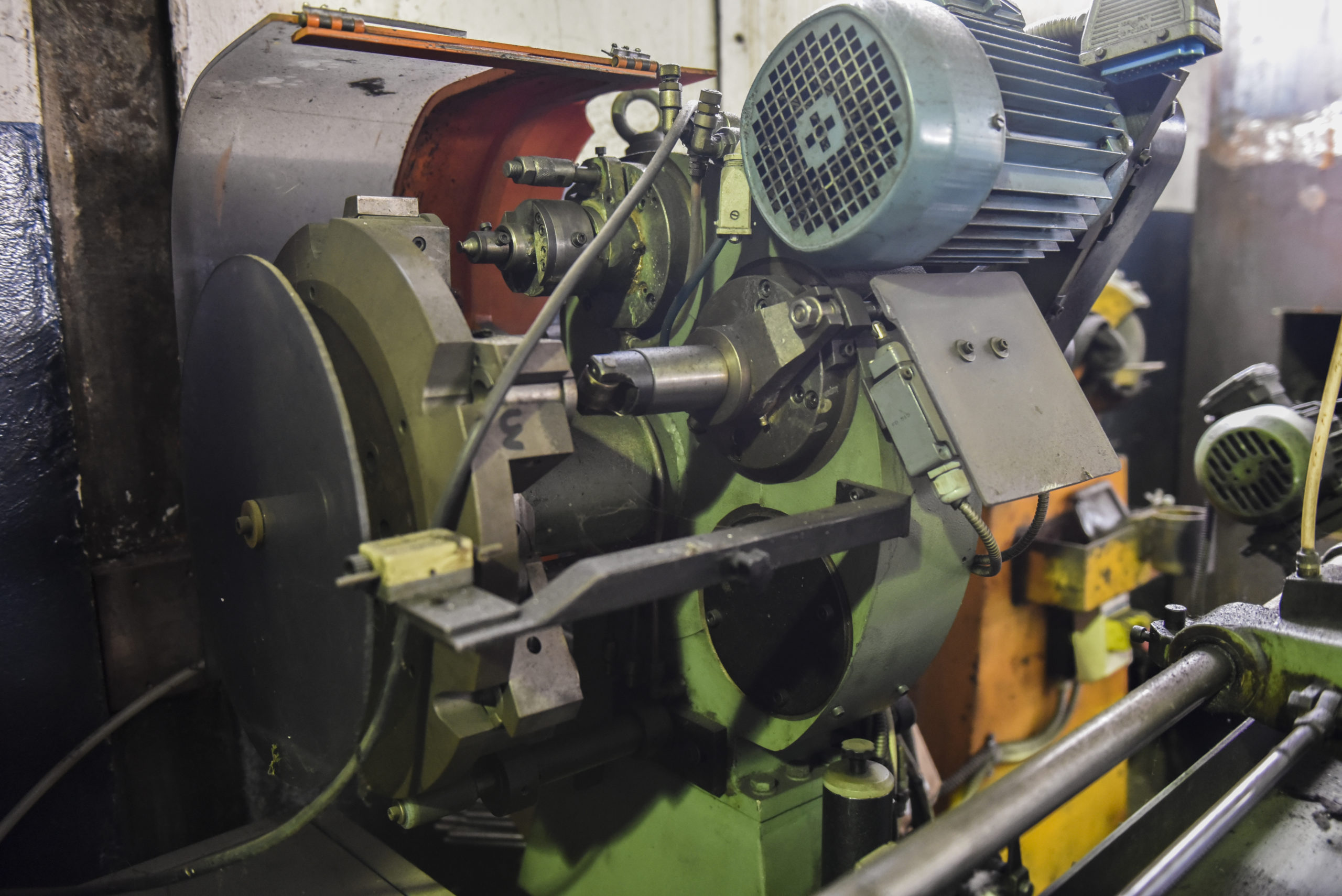
Sustainability in production
The year 2022 marks the official publication of a second Grazioli patent. After the one filed in 1975, we received approval for the work units to be applied to our electromechanically operated transfer system, to reduce the amount of mineral oil needed to operate the system.
A technological choice that pushes mechanics towards a new frontier of sustainability, a sustainability that day after day aims at becoming a quality standard of excellence.
Introducing sustainability into the production sector has been a major challenge for all of us. The days of planning, study and research involved the management, designers and operators who every day build, piece by piece, the machinery for our customers. To say that it was easy would be lying, but this did not frighten us; on the contrary, it allowed us to put all our technical know-how into play and learn new skills.
Innovation makes sense if it brings benefits and respects the development of future generations. This has been the philosophy with which we have pursued the process of sustainability in the production sector. We have a long way to go and there is still a lot we can do in this respect, but we are ready for it and we are not afraid of challenges, especially since the well-being of everyone is at stake.